

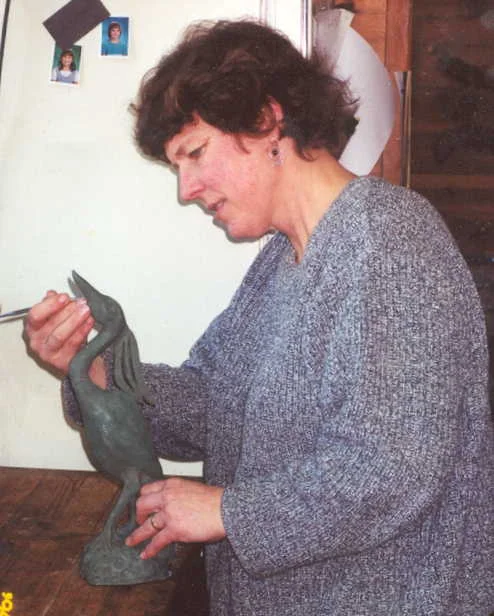
sculpturing clay

Wax in Mold

Wax work

Sculpture sprued
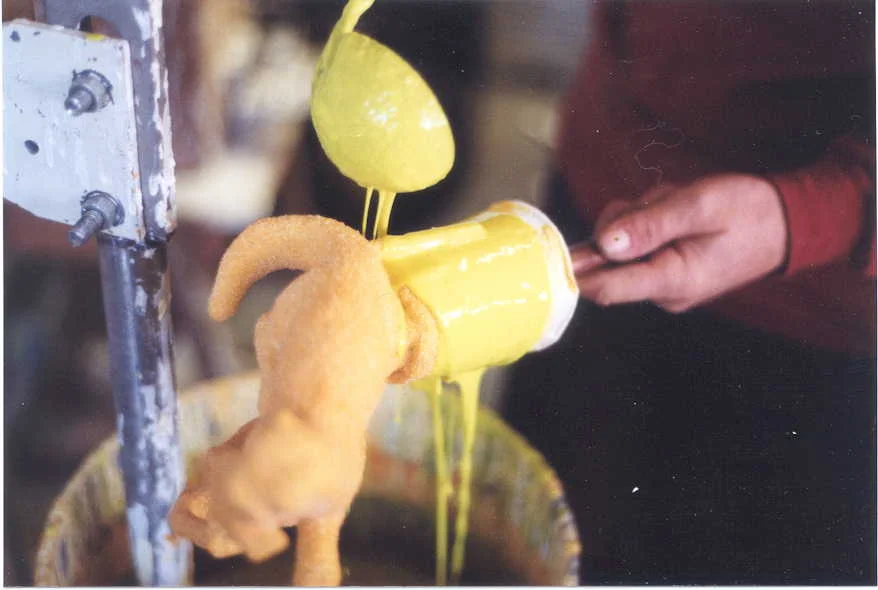
Slurry
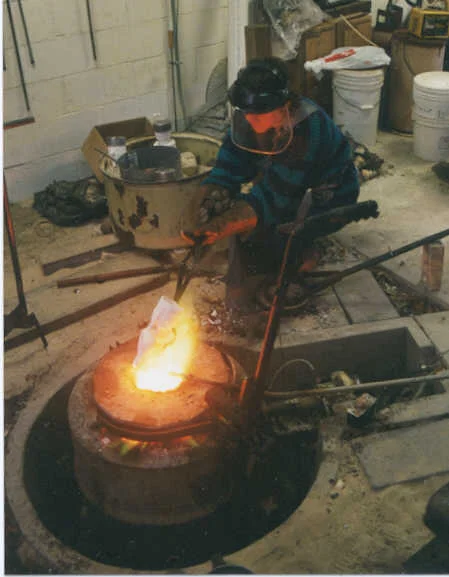
Flash burnout

info
1
2
3
4
5
6
7
8
9
·
·
·
·
·
·
·
·
·





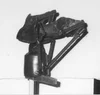
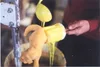

